3 Common Causes of Weld Spatter
Weld spatter represents one of the more common problems associated with welding. It involves the accumulation of small bits of molten metal thrown out of the weld area during welding. As these particles dry, they become stuck to the metal next to the weld - giving it a rough, stubbly, and often sharp feeling.
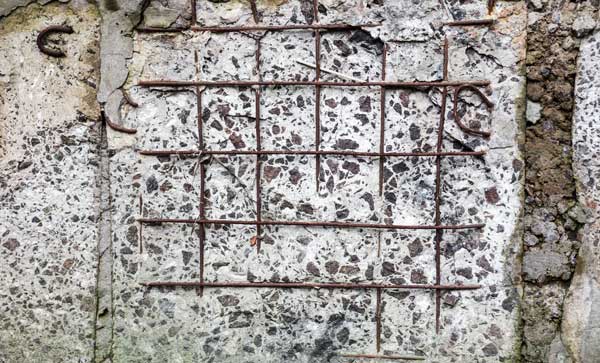
While weld spatter does not constitute a serious structural problem, it will significantly mar the appearance of the weld. Not only that, but it may pose a risk of bodily harm when present on things like handrails. In some cases, weld spatter may also increase the risk of corrosion eating away at the base metal.
Unfortunately, many inexperienced welders fail to understand the causes of weld spatter. This makes them somewhat helpless when it comes to preventing spatter. If you would like to increase your knowledge of weld spatter, read on. This article will discuss three of this issue's most common causes.
1. Improper Weld Settings
Successful welding requires carefully controlling a number of different factors. Failing to set these properly may prevent the weld from occurring at all. In other cases, however, improper settings may lead to an unacceptable level of weld spatter. There are three important factors to be aware of when dealing with gas metal arc welding, which is one of the most commonly used welding styles.
The first factor involves the amount of amperage being used. Excessive amperage tends to cause weld spatter. Amperage can be lowered to safe levels in one of two ways: either slowing down the wire feed speed or increasing the voltage. Assuming wire feed speed is within an appropriate range, the problem often stems from insufficient voltage.
The third factor that increases the risk of weld spatter has to do with a term known as electric stick out, or ESO. ESO simply conveys the distance between the tip of the welding contact and the surface of the metal. Weld spatter tends to occur more when ESO is too high - in other words, when the distance between contact and metal remains too large.
2. Excessive Work Angle
The work angle refers to the angle between the welding torch and the surface of the metal. This angle plays a key role in the behavior of the weld. In particular, problems tend to result from work angles greater than 15 degrees. Such an angle tends to promote a greater amount of gas flow.
In other words, angles in excess of 15 degrees will act to draw air toward the torch from behind. This air will then come in contact with the still-molten puddle of welding material. If the force of the air happens to be strong enough, it will lead to weld spatter. The molten metal will literally be blown away from the weld in the form of tiny droplets.
3. Dirty Weld Surface
The cleanliness of the weld surface will have a large effect on whether or not weld spatter occurs. The more contaminants are present, the greater the chances of spatter. For this reason, experienced welders know that metals must be pre-treated prior to welding.
The pre-treating process involves carefully cleaning the metal with a degreasing substance. This acts to remove any traces of dirt, oil, or other surface contaminants. Any surface rust must also be carefully removed. The weld area itself should also be cleaned using a grinder. This will reveal a fresh layer of metal - promoting a cleaner bond and reducing the chances of spatter.
At its heart, welding is a relatively simple process. However, the number of different variables involved in getting the right results means that welding jobs should always be undertaken by experienced professionals. For more information about what it means to weld the right way, please don't hesitate to contact the pros at 3-B Welding, LLC.
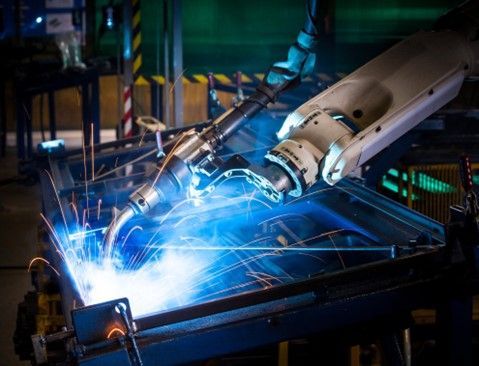